Стоимость оборудования
для переработки ртутных ламп
от 1700000 рублей
в зависимости от комплектации, скорости и объема переработки.
Так же как в результате естественной эволюции техники и технологии в наши дома и квартиры пришли стиральные машины, котлы, газовые обогреватели, электростанции и другое оборудование, ранее считавшееся объектом повышенной опасности и отделявшееся от жилой застройки санитарно-защитными зонами, к переработчикам и потребителям люминесцентных ламп пришли малогабаритные установки и миниатюрные аппараты для ручной демеркуризации низкой и сверхнизкой стоимости.
Многофункциональная «Установка разделения компонентов, обезвреживания и утилизации ртутьсодержащих ламп и отходов «Экотром-2У» разработана в 2011 году (ТУ 3618-81835672-001-2015 взамен ТУ 3647-001-29496068-2011), декларация о соответствии TC N RU Д-RU.AЯ24.B.03347 от 17.03.2015, санитарно-гигиеническое заключение на технологию и установку «Экотром-2У» института им. А.Н. Сысина).
В основу обезвреживания (демеркуризации) на установке положена технология обработки измельчаемых частей ламп раствором химического демеркуризатора Э-2000Т с нейтрализацией ртути в сульфидной форме. (Отчет №15/169-07 ГУ НИИ Экологии человека и гигиены окружающей среды им. А.Н. Сысина).
Отходы:
цоколи - IV класса опасности утилизируются;
стеклобой, включающий демеркуризированный люминофор – IV класса опасности размещается на полигонах ТБО;
стоков и жидких ртутьсодержащих отходов нет.
Уборка оборудования и помещения осуществляется влажным способом.
Эксплуатационные (расходные) материалы
Уголь активированный. Расход не более 6 кг в год;
Препарат демеркуризационный Э-2000Т. Расход 2 литра на 1000 средних прямых ламп и 2,2 литра на 1000 средних компактных люминесцентных ламп и горелок.
Установка изготавливается в климатическом исполнении категории УХЛ 4 по ГОСТ 15150-69 для эксплуатации в помещениях, мобильных (инвентарных) зданиях контейнерного типа, модулях, боксах, как имеющих собственную ходовую часть, так и не имеющих собственной ходовой части при температуре от +12°С до +28°С и относительной влажности не более 80%.
Минимальная площадь размещения установки с зоной обслуживания – 4,5 м² (при условии обслуживания одним работником).
ТЕХНИЧЕСКОЕ ОПИСАНИЕ И ТЕХНОЛОГИЯ ДЕМЕРКУРИЗАЦИИ
Аппараты измельчения (4) и сборники-накопители отходов (3) расположены в тупиковой, не продуваемой части установки и воздух поступающий через загрузочные трубы (4.8; 4.2) и создающий в аппаратах измельчения (4) необходимое разряжение удаляется в узел очистки технологического воздуха и затем в атмосферу практически не контактируя с измельчаемыми в присутствии раствора препарата Э-2000Т ртутьсодержащих ламп.
Загрузочная труба (4.8) оснащена устройством, регулирующим все технологические процессы, осуществляемые в установке.
При загрузке прямых ламп, во входной конус трубы (4.8) вводятся сменные конические вставки, соответствующие диаметрам загружаемых ламп. В результате ввода лампы в коническую вставку скорость обтекающего лампу воздуха достигает 80 – 100 м/сек и в загрузочной трубе (4.8), аппарате измельчения (4) и сборнике-накопителе (3) разряжение увеличивается до 400 мм в.ст.
В результате этого кратковременного, длящегося менее 0,1 секунды (время прохождения лампы через коническую вставку), скачка разряжения:
в аппарат измельчения (4) из емкости (4.10) засасывается раствор демеркуризатора в объеме соответствующем длине и объему загружаемой лампы;
вводимая лампа резко ускоряется и разрушается в аппарате в момент поступления раствора;
возникающие при вращения ударных элементов, горизонтальные и вертикальные вихри интенсивно перемешивают измельчаемые части ламп, с поступающим раствором и выбрасывают смесь через патрубок (4.3) в сборник обезвреженных отходов (3), в котором продолжаются процессы разложения препарата до полного высыхания смеси;
на поверхности измельченного стекла и других материалов в вихревых потоках влажного теплого воздуха происходят процессы разложения полисульфида и тиосульфата кальция с высвобождением высокоактивной дисперсной серы, а так же высокоактивного в этих условиях сероводорода (до 2 мг/м³) которые взаимодействуя со ртутью сорбированной люминофором и ртутью, находящейся в состоянии пара переводят ее в сульфидную форму, а за счет тепла высвобождаемого в процессе гидролиза полисульфидов в паровой фазе все находящиеся в сборнике обезвреживаемые отходы высушиваются;
накопившиеся в реакционной зоне за последние 5 – 6 секунд (интервал между загрузками) пары ртути до 0,006 мг/лампа, сероводород (до 2 мг/м3), пары воды и твердые аэрозоли (˂ 50 мкм) поступают (в объеме от 0,2 до 1,5 литров на одну лампу) в выводимый из загрузочной трубы технологический воздух и направляются в узел очистки. Концентрация паров ртути в удаляемом на очистку воздухе достигает 0,07 мг/м³ (для ламп L - 1200мм Ø 32мм, при интервале загрузок 6 сек).
При измельчении и обработке прямых ламп концентрация паров ртути тем выше, чем лампа длиннее (скачок разряжения продолжительнее) и чем больше диаметр лампы (больше объем вытесняемого воздуха при движении в загрузочной трубе).
При измельчении и обработке компактных люминесцентных ламп, концентрация паров ртути в удаляемом на очистку воздухе не превышает 0,001 мг/м³. Для сравнения концентрация паров ртути 0,001 мг/м³ (1мкг/м³) – это ПДК в атмосферном воздухе населенных мест в Европейском союзе, рекомендована так же Всемирной организацией здравоохранения.
Все относящееся к обработке прямых ламп в аппарате для прямых ламп относится и к аппарату измельчения только КЛЛ, с той разницей что скачок разряжения в аппарате измельчения и сборнике-накопителе незначителен (50-100 мм в.ст.), а обрабатываемая лампа диаметром свыше 65мм., вводимая в загрузочную трубу (4.2) при помощи специального приспособления (4.6) предварительно окунается в емкость (4.10) с раствором демеркуризатора расположенную под загрузочной трубой.
КЛЛ диаметром до 65мм. вставляется цоколем вверх в отверстие, проделанное в пластиковой пластине. Цоколь вставленный в отверстие придерживается рукой, а пластина с удерживаемой лампой прижимается к торцу загрузочной трубы. При этом доступ воздуха в установку на одну две секунды (определяется опытным путем)прекращается; в измельчителе (4) возникает вакуум, за счет которого раствор через прозрачную трубку (процесс очень нагляден) поступает в аппарат измельчения; лампа придерживаемая рукой отпускается, а через освобожденное отверстие возобновляется доступ воздуха в установку.
Циклон (2.1), как основной аппарат очистки от твердых аэрозолей выбран из-за его высокой эффективности по отношению к стеклянной пыли и люминофору (>99,5%). Вторым существенным качеством циклона является постоянная величина его сопротивления и третьим – отсутствие контакта поступающих веществ с предшествующими (как это происходит при фильтрации), которые в доли секунды обезвреживаются раствором демеркуризатора в сборнике (2.1.1), расположенном под циклоном.
Окончательная химическая очистка технологического воздуха осуществляется в адсорбере (2.2), заполненном активированным углем модифицированным серой, хлором или йодом. Химическая очистка должна обеспечивать концентрацию паров ртути в выбросах не превышающую 0,005 мг/м³ для установки в I комплектации и <0,0003 мг/м³ для установок II и III комплектации.
В 1 кг измельченного и обработанного демеркуризационным препаратом Э-2000Т стеклобоя по данным исследовательских лабораторий содержится не более 50 мг ртути в виде сульфида или примерно 6 мг на одну люминесцентную лампу включая КЛЛ. Учитывая, что в газоочистной тракт установки от каждой лампы поступает в среднем 0,006 мг ртути, в стеклобое ее остается 99,9% в виде сульфида и только 0,1% поступает на очистку. Это подтверждается при инструментальных замерах.
ДОКУМЕНТАЦИЯ НА УСТАНОВКУ
Руководство по эксплуатации установки "Экотром-2У"
Технические условия ТУ 3618-001-81835672-2015
Декларация о соответствии TC N RU Д-RU.AЯ24.B.03347
Санитарно-гигиеническое заключение ГУ НИИ экологии человека и гигиены окружающей среды им. А.Н.Сысина - 2015г.
Заключение ГЭЭ
Протокол оценки физических факторов рабочей зоны (шума)
Протокол количественного химического анализа промышленные выбросы
Протокол количественного химического анализа воздуха рабочей зоны
Протокол испытаний
ТУ на препарата
ТУ на отходы
СЭС на препарата
СЭС на отходы
Если Вы хотите купить установку "Экотром-2" (ТУ 3647-001-29496068-2006), предназначенную для переработки и обезвреживания всей номенклатуры линейных (прямых) и компактных энергосберегающих ртутьсодержащих люминесцентных ламп. Принцип действия установки основан на разрушении ламп и разделении их на компоненты - стеклянный бой, лом черных и цветных металлов и ртутьсодержащий люминофор. Выделенные в процессе разрушения компоненты раздельно собираются в транспортные технологические сборники. Модульное построение узлов установки позволяет размещать установку на различных по своей конфигурации площадях. Установка «Экотром-2» защищена патентами РФ и отвечает всем санитарно-гигиеническим требованиям, связанным с промышленным ведением работ с ртутьсодержащими отходами. Установка "Экотром-2" прошла государственную экологическую экспертизу.
ОСНОВНЫЕ ТЕХНИЧЕСКИЕ ХАРАКТЕРИСТИКИ
Производительность – до 1200 ламп/час;
Энергопотребление –не более 12 кВт/час;
Производственная площадь – 20 м2.
БАЗОВАЯ КОМПЛЕКТАЦИЯ УСТАНОВКИ "ЭКОТРОМ-2"
Узел загрузки прямых и компактных ламп;
Модуль 1 - разделения ламп на компоненты;
Модуль-2 - обезвреживание ртутьсодержащего люминофора;
Модуль 3 - очистки воздуха от ртутных паров.
Технология переработки ртутных ламп, переработка отходов
Принцип действия так называемой «холодной и сухой» вибропневматической установки «Экотром-2» основан на разделении ртутных ламп на главные составляющие: стекло, металлические цоколи и ртутьсодержащий люминофор. Очищенные от ртути стеклобой и металлические цоколи (алюминиевые и стальные) используются как вторичное сырье. Люминофор также является сырьем для получения ртути на специализированных предприятиях( например на ртутном руднике ЗАО НПП «Кубаньцветмет») или на малогабаритных установках типа УРЛ-2М производства ФИД-ДУБНА.
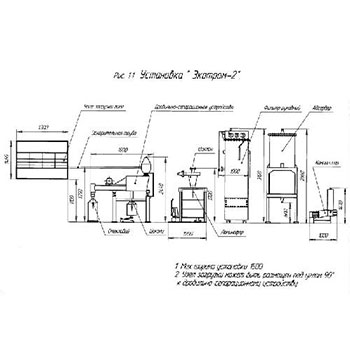
Установка состоит из двух основных блоков: устройства разделения ламп, состоящего из узла загрузки, пневмо-вибрационного сепаратора с дробилкой, циклона и системы очистки, включающей в себя фильтр рукавный, адсорбер и газодувку с компрессором. Компрессор создает в установке разряжение по всему тракту с 5-8 КПА (в зоне загрузки ламп) до 19-23 КПА перед газодувкой, что обеспечивает безопасность работы на установке, так как исключаются пылевоздушные выбросы в производственное помещение.
Переработка ртутных ламп на установке «Экотром-2 проводится следующим образом:
Доставленные в специальных контейнерах (бочки из оцинкованного железа с чехлами) ртутные лампы подаются в узел загрузки.
За счет высокого разряжения в пневмо-вибрационном сепараторе лампы одна за другой непрерывно подаются в ускорительную трубу, попадают в дробилку и измельчаются до крупности стекла до 8 мм.
Цоколи отделяются от стекла на вибрирующей решетке и удаляются в сборник – технологический контейнер. Заполненный цоколями технологический контейнер направляется в демеркуризационно–отжиговую электрическую печь, газовые выбросы из которой поступают в систему очистки. В результате термической обработки цоколи полностью очищаются от остаточных загрязнений ртутью. Доочистка цоколей от ртути может быть осуществлена также на установке УРЛ-2М.
Отделение люминофора – главного носителя ртути, от стекла осуществляется за счет выдувания его в противоточно движущейся системе «стеклобой-воздух» в условиях вибрации. Очищенное от люминофора стекло поступает в бункер-накопитель. Конструкция пневмо-вибрационного сепаратора с дробилкой обеспечивает в процессе работы очистку стекла от ртути до величин значительно меньших ПДК ртути в почве 2,1мг/кг. Основная масса люминофора улавливается в циклоне и попадает в сборник люминофора (представляющий собой транспортную металлическую бочку с полиэтиленовым мешком-вкладышем и специальной крышкой). Остальные 3-5% люминофора осаждаются в приемнике рукавного фильтра и в дальнейшем также упаковываются в транспортные металлические бочки.
Воздушный поток последовательно очищается от люминофора в циклоне, рукавном фильтре и адсорбере. Очистка воздуха от паров ртути происходит в адсорбере до содержания ртути в воздухе менее 0,0001 мг/м3. При превышении содержания ртути значения ПДК в выбросах в атмосферу производится замена отработанного активированного угля в адсорберах. Вместе с люминофором в металлические бочки с полиэтиленовым вкладышем упаковывается отработанный активированный уголь, а также загрязненная обтирочная ветошь.
Вода после санитарной обработки помещения и периодической демеркуризации установки, скапливаемая в футерованном приямке, идет на смачивание люминофора.
Работа на установке ведется под постоянным аналитическим контролем аккредитованной лаборатории на содержание ртути в стеклобое, цоколях и в люминофоре. Определяется содержание паров ртути в воздухе рабочей зоны и на выходе воздушного потока из адсорбера в атмосферу. Анализы проводятся с помощью приборов АГП-0,1 с термоприставкой. (Аттестат аккредитации лаборатории № РОСС PU. 0001. 511150.) .
Основные характеристики установки, ее сертификация и применение
Производительность установки (в час)
1. Отработанные лампы-1200 шт.
2. Стеклобой-250-280 кг
3. Люминофор-15-18 кг
4. Цоколи-5 кг
Необходимо отметить очень высокую производительность установки «Экотром-2» по сравнению с «термическими» и «гидрометаллургическими» способами. Производительность установки «Экотром-2» по переработке ламп составляет 1200 штук в час. При этом в среднем получается вторичного сырья за час работы установки:
Стеклобоя 250-280кг
Люминофора 15-18кг
Цоколей 5кг
Энергопотребление установки и расход материалов
Электроэнергия-11 квт/ч (в т. ч. газодувка-7,5 квт/час, дробилка-2 квт/час, вибратор-1,1 квт/ч, прочие-0,4 квт/час)
Активированный уголь (адсорберы)-0,5 т/год
Сжатый воздух (продувка рукавных фильтров)-0,3 м3/час
Санитарная обработка-20 л/смена
Расход электроэнергии на работу установки составляет 11кв/ч.
Необходим сжатый воздух для продувки рукавных фильтров, вода для периодической санитарной обработки установки и примерно 0,5 тонн активированного угля в год для адсорберов.
Для размещения установки необходима площадь не менее 20 м² в производственном помещении.
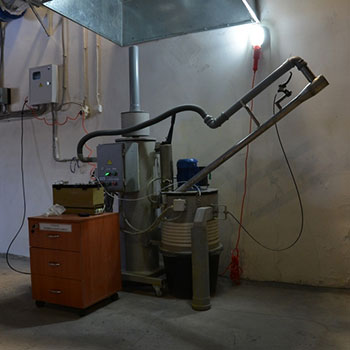